Analysis for carburization behavior of low-carbon steel during smelting process
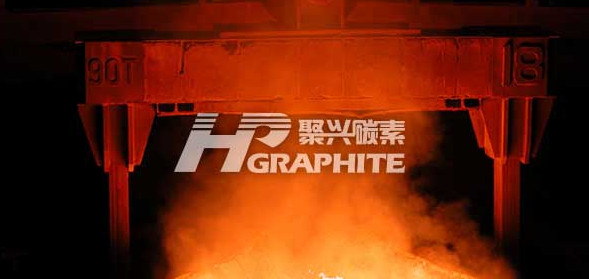
Analysis for carburization behavior of low-carbon steel during smelting process
The reasons of carburization of low - carbon steel during the refining process were analyzed by applying the fault tree theoretical analysis method. The improvement measures including adjusting the inclination angle of the conductive arm to balance the reactance of three-phase current and reduce the electrode consumption, adjusting the supply amount of argon gas and the angle of the bottom blowing hole for argon gas to mix the molten steel and save the mixing time, adjusting the ration of the coarse aggregate in the formula for the graphite electrode to reduce the cracking and chip off-falling of the electrodes, were put forth, which could provide the technological support for reducing the carburization of low-carbon steel during the refining process.
The fault tree analysis method is an analysis method pioneered by NASA in the 1970s when launching rockets to find accident points. Since this method can be used for not only qualitative analysis but also quantitative analysis, it is widely used in accident prediction and accident handling. The core technology of refining furnace to smelt low-carbon steel is to control the source of carbon. There are many reasons for the carbon increase of low-carbon steel, including the carbon from the converter, the quality of the graphite electrode, the damaged magnesia carbon brick carburization of the refining package, the power supply equipment of the LF furnace, the argon gas flow, and the angle of the argon pores, etc. Therefore, it is very difficult to accurately find the carbon increase point of low-carbon steel in actual production. This article uses the accident tree analysis method to analyze and discuss the root causes of low-carbon steel carbon increase in the refining stage.
1 Application of fault tree analysis method to analyze the root causes of carbon increase
Extract the carbon increase data from the actual smelting work data table, and establish the data source of the fault tree.
(1) The carbon from the converter and refining carbon increase index data (Table 1)
It can be seen from Table 1 that the carbon from the converter index shows that the higher the carbon from the converter content, the more likely it is to cause the molten steel carbon of low-carbon steel to exceed the standard. Regardless of the carbon level of the converter, the carbon increase rate in the total of 237 furnaces of molten steel is 0.01%~0.02%, which accounts for more than 93% of the total molten steel, indicating that the phenomenon of molten steel carbon increase in the refining process is common.
(2) Data extraction of current, consumption of each phase and electrode inclination of three-phase graphite electrode (Table 2)
From the data analysis of the current and consumption of each phase of the three-phase electrode in Table 2, the current of the A-phase electrode is 1.4 times higher than that of the B-phase and C-phase, and the consumption of the A-phase electrode is 1.6 times higher than that of the B-phase and C-phase. The root cause of this phenomenon is the imbalance of reactance caused by the different electrode inclination angles (phase A is regarded as abnormal consumption, and phase B and C electrodes are regarded as normal consumption).
(3) Power-on time and low-carbon steel carbon increase data extraction (Table 3)
It can be seen from the power-on time in Table 3 that the longer the smelting power-on time, the easier it is for the molten steel to be carbonized. When the smelting time is less than 16 minutes, the contribution rate of the furnace with excess carbon is 0, so the carbon increase within 16 minutes can be regarded as normal carbon increase talk with us to get more related guidance.
(4) Data extraction of argon bottom blowing flow rate and bottom blowing angle (Table 4)
No related results found
0 Replies