How to improve anti-oxidation property of graphite materials? Water-soluble impregnant
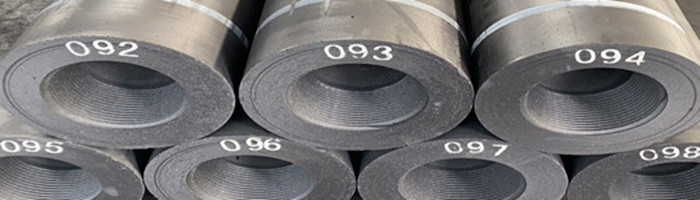
How to improve anti-oxidation property of graphite materials? Water-soluble impregnant
Graphite materials have very specific properties such as good electrical and thermal conductivity, self-lubricating, low hardness, low friction, high temperature resistance, etc., and have a wide range of applications in metallurgy, electrical, electronic, mechanical, chemical, and nuclear industries. However, graphite materials also have obvious shortcomings, that is, insufficient oxidation resistance. Graphite materials start to oxidize slightly at about 450 ℃ in an aerobic environment, and oxidize violently at about 750 ℃. Therefore, when graphite is used as a high-temperature material, it is generally used in an oxygen-less or oxygen-free environment, and it can only be used as a consumable material when it is aerobic.
In order to broaden the application range of graphite materials, scientists at home and abroad have conducted a lot of research on the oxidation resistance of graphite materials, and have obtained many methods to improve the oxidation resistance of graphite materials, such as: solution dipping, coating, self-healing, and carbon-ceramic composite method. However, the above methods have their own shortcomings. For example, the coating method is relatively expensive, and is generally only suitable for products with a small amount and high added value, and the thermal expansion coefficient between the coating and graphite material is difficult to match, and they are easy to fall off under severe temperature changes. The self-healing method generally oxidizes the ceramic particles added to the graphite substrate to form a ceramic film on the surface, so that the surface of graphite material has some ceramic material properties, which must have an impact on the hardness of graphite material, self-lubrication and other properties.
The solution immersion method has little effect on the properties of graphite materials, but the oxidation resistance is not as good as that of coating method and carbon-ceramic composite method. Therefore, all the above methods have their advantages and disadvantages, the specific choice needs to see the environment of graphite material service. See More GE products information.
Relatively speaking, the impregnation method has the characteristics of low investment, low cost, simple process, strong adaptability, and less environmental pollution. It is an effective way to improve the oxidation resistance of graphite materials and has obvious economic benefits. Solvents commonly used in the impregnation method can be divided into two categories: organic solvents and water. Organic solvents are mostly flammable and toxic solvents such as toluene and xylene. Environmental protection is under great pressure in use. Therefore, pollution-free water is used as a solvent to prepare antioxidants. Impregnant. In this paper, magnesium dihydrogen phosphate and aluminum dihydrogen phosphate are used as the main impregnants. By adding different mass fractions of phosphoric acid, boric acid and other raw materials, a graphite material antioxidant impregnant with excellent performance and convenient use is prepared, and the antioxidant activity of this kind of antioxidant was studied under 1 000 ℃.
1 Test
1.1 Sample preparation
The graphite material for the test was sampled from the Φ318 mm joint of the ultra-high-power graphite electrode produced by Kaifeng Carbon Co., Ltd., and the sample was made into a cylinder of Φ25 mm × 30 mm. The bulk density of the sample is 1.85 g/cm3, the apparent porosity is 15%, and the resistivity is 3.3 μΩ·m.
1.2 Preparation of impregnant
Take a certain amount of deionized water, phosphoric acid, magnesium dihydrogen phosphate, aluminum dihydrogen phosphate, and sodium hexametaphosphate in a beaker, heat it to about 70 ℃, add the weighed boric acid under stirring, and prepare it to become colorless and transparent liquor, and then add a small amount of glycerol as a surfactant.
1.3 Test equipment
Electronic analytical balance: division value is 0.1 mg;
Electric heating constant temperature blast drying oven: model 101-3, working temperature RT~300 °C;
Box-type resistance furnace: working temperature RT~1 200 ℃;
Thermal analyzer: TG/DSC;
Water ring vacuum pump.
2 Test and results
2.1 Differential thermal-thermogravimetric analysis of antioxidant impregnant
Take a small amount of impregnating agent in a 100 mL beaker and keep it at a constant temperature of 110 °C for 4 h. At this time, the impregnating agent becomes a paste. Take a small amount of paste-like anti-oxidant impregnant for differential thermal-thermogravimetric analysis, and the results are shown in Figure 1.
It can be seen from Figure 1 that there is a wide endothermic peak A between 120 ~ 150 ℃, which may correspond to the removal of solvent water and crystal water remaining in the impregnant, and H3BO3 forms water molecules lost by metaboric acid or pyroboric acid when heated. With the increase of temperature, there is an absorption peak B near 220 ℃, which may be the endothermic peak formed by the thermal decomposition of metaboric acid or pyroboric acid in the impregnant to generate B2O3 and a small amount of glycerin. When the temperature continues to rise, the remaining components in the impregnant will undergo polycondensation reactions with each other, the water molecules and other small molecules in it will volatilize, and the quality will continue to decrease. However, when the temperature is higher than 400 ℃, the rate of mass reduction slows down, indicating that the reaction between the components in the impregnant is basically completed after the temperature is higher than 400 ℃.
2.2 Impregnation and heat treatment process
The contaminants and floating ash layer on the surface of the prepared sample are removed, and then placed in an ultrasonic cleaner for ultrasonic cleaning for 20 min, and then dried in an oven at a constant temperature of 120 ℃.
In order to study the influence of vacuum degree and immersion time on the immersion effect during immersion, the samples were divided into 5 groups, 3 samples in each group were subjected to an immersion-oxidation resistance experiment, and all samples were subjected to the immersion-heat treatment process twice. See Table 1 for sample grouping. The specific immersion process is as follows: When the vacuum immersion is not applied, the immersion liquid is heated to 65 ℃, and the dried sample is placed in the immersion liquid. The time the sample is immersed in the immersion liquid is carried out according to Table 1. When vacuuming and impregnating, the degree of vacuum is maintained at -0.09 MPa, and the vacuum holding time is executed in accordance with Table 1. After that, the vacuum is broken and the sample is taken out.
After all the samples were soaked, they were placed in an oven to dry. The drying step was 90 °C for 3 hours, and then the temperature was raised to 110 °C for 3 hours. After the sample is dried, heat treatment is carried out. During the heat treatment, N2 must be used as a shielding gas during heat treatment. The maximum temperature of the heat treatment is 800 ℃, after which the temperature is kept for 30 minutes. After the heat preservation is completed, the temperature is naturally cooled to below 400 ℃, and the protection gas can be stopped. After the temperature drops to room temperature, the sample is taken out, weighed, and the weight gain rate is calculated.
No related results found
0 Replies