Two baking technologies of graphite electrodes discussion
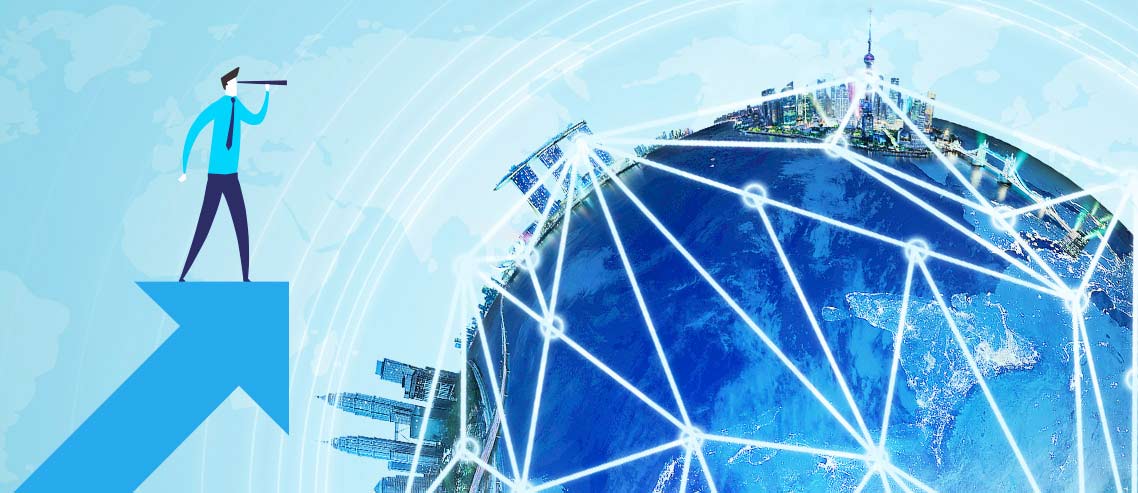
Two baking technologies of graphite electrodes discussion
1 Physical and chemical indicators of the product
The bulk density of the products baked in the ring furnace is very different at both ends, the maximum is 0.048 g/cm3, and the average is about 0.034 g/cm3, while the car bottom furnace is within 0.023 g/cm3. For the whole product, the product baked in the ring furnace has obvious differences in both bulk density, strength and resistivity at both ends of the product, as shown in Figure 1.
The two processes have different temperature fields during heating. The car bottom furnace is for the products to be installed in the saggers, which are placed in a closed space for heating (3 heating zones), and are stirred by a circulating fan. The temperature difference in the furnace atmosphere is kept within 20 ℃. The ring furnace is one or several flame systems composed of multiple furnace chambers continuously operating. There are not only temperature differences in the horizontal direction among several bins in a furnace chamber, but also large temperature differences in the vertical position, and some even reach nearly 250 ℃. The greater the temperature difference, the more obvious the difference in the heating rate between the upper and lower ends of the product, which often exceeds the temperature rise control requirements of the product, resulting in increased inhomogeneity of the product. The actual temperature measurement of the product shows that the temperature difference between the upper and lower ends of the car bottom furnace is below 15 ℃ within the critical temperature of 250 to 450 ℃, while the ring furnace is significantly higher than the car bottom furnace, reaching more than 6 times. The difference in the heating rate of each part of the same electrode will cause the migration of pitch, the volume expansion and contraction of the product during the baking process, the decline of the physical and chemical properties of the baking product, and affect the production of graphitization in the subsequent process.
2 The internal quality of the product
A sample was drilled from the center of the upper and lower ends of the product, and it was found that the sample baked in the ring furnace often appeared loose and cracked at one end, and the cracks were obvious after the flat end, as shown in Figure 2 (a), (c). For the electrodes baked in the car bottom furnace, the upper and lower ends of the sample and the flat ends are compact in appearance, and there is no obvious difference, as shown in Figure 2(b), (d).
During the baking process, the raw product undergoes the stages of pitch softening, pyrolysis, aggregation, and coking, which correspondingly cause the expansion and contraction of the product, and the internal cracks are extremely easy to produce. Such cracks cannot be compensated even if impregnated. The poor thermal conductivity of the raw product causes the outside of the product to solidify before the inside, hinders the elimination of volatiles, and causes extremely high stress inside the product. When the size of the electrode increases, the heating rate in the critical temperature area should be smoothly reduced to extend the firing curve, such as the production of 0800 mm ultra-high power graphite electrodes.
For ultra-high-power graphite electrodes with specifications of Φ600 mm and above, they must experience a high temperature of more than 3 000 ℃ during the production of graphitization in series with internal heat, and the heating speed is also very fast. After graphitization, the defects of the products with baking defects will expand to different degrees, which will make the overall quality of the products deteriorate and even cause longitudinal crack waste products. Moreover, the products are also prone to crack the hole wall, break off the hole bottom or fall off during the use of steelmaking.
3 Conclusions and recommendations
1) The superior temperature field of the car bottom furnace enables the products to be heated according to the set heating system (product temperature) during the baking process, which is conducive to the uniform quality of the products in the radial and longitudinal directions. However, due to the large temperature difference and the inconsistent heating rate of the products in the ring baking furnace, the physical and chemical properties of the two ends are significantly different, and the internal stress of the product increases, which is likely to cause cracks in the product.
2) Large-size ultra-high-power graphite electrodes require high performance indicators, reducing the temperature difference of the product during the baking process, reducing the difference in quality between the upper and lower ends of the product, increasing the graphitization yield, and reducing the hole wall damage accident in steelmaking applications.
3) During the baking process of ultra-high power graphite electrode products, the pyrolysis and polycondensation behavior of carbon paste and binder pitch are very different. Needle coke in the carbon paste has an important influence on the pyrolysis and polycondensation behavior of binder pitch. Needle coke in the paste changes the pyrolysis and condensation behavior of pitch. It is recommended that in the production of graphite electrodes, the TGA test of the carbon paste should be carried out for different baking equipment to develop the temperature rise curve of the key temperature zone. The TGA test of carbon paste is more representative than the TGA test of binder pitch.
4) For the baking of large-size ultra-high power graphite electrodes, the car bottom furnace process is one of the best baking methods. Extending the baking curve can improve the internal quality of the baked product.
No related results found
0 Replies